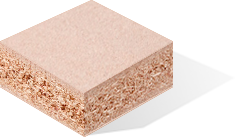
Particle board production plants
The wooden material is first selected and separated from foreign bodies, and then it is grounded and reduced to "chips" of appropriate size, which are dried by means of a rotating drum dryer. The material is brought into the drum by a stream of hot air, which transfers heat mainly by convection. At the drum outlet an accurately dimensioned settling chamber allows the separation of the “coarse” fraction of the dried material. The “fine” dried material on the other hand is conveyed to and separated by a battery of new-concept LPD cyclones. The material is then mixed with glue and sent to the forming machines which create the "mattress" of the panel, which will be later hot pressed and then finished by edge trimmers, sanders and cutters. Such particle board is characterized by a multi-layer structure or, rather, by the so-called "continuous variable grain size” (finer chips are placed on the outer panel sides, while bigger chips on the inner side).
Advantages Particle board production plants
Excellent performance and resistance to wear, even in case of use of recycled wood
Pre-integrated dryer (either Omega or Gravimetric Separator)
Automatic extraction system of silice
Fan installed after the cyclones
Gallery
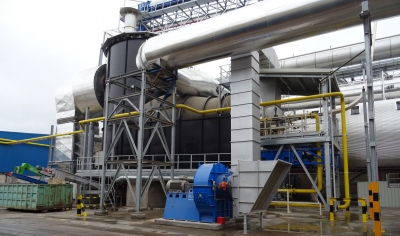
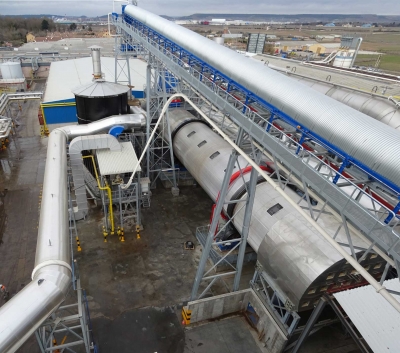
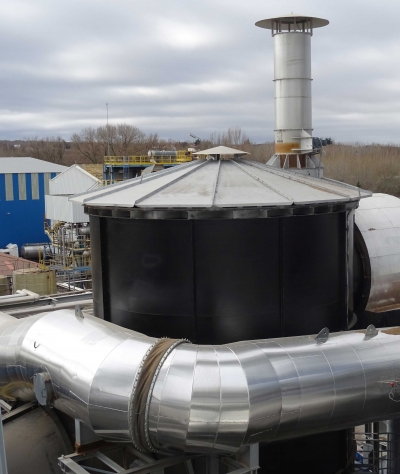
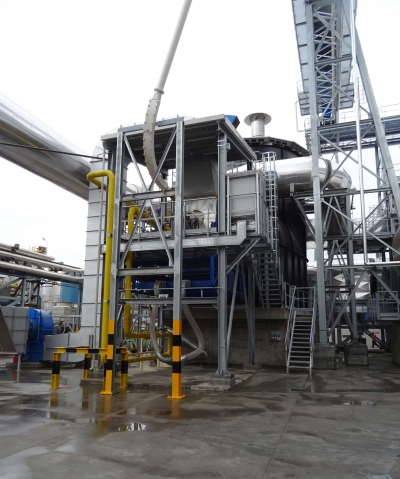
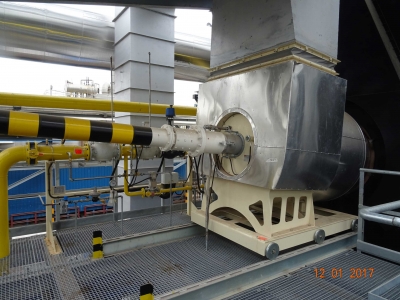
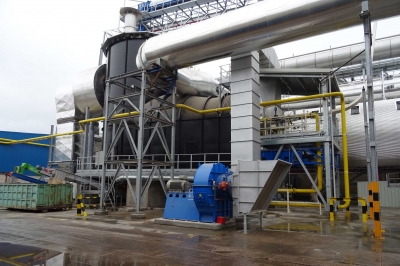
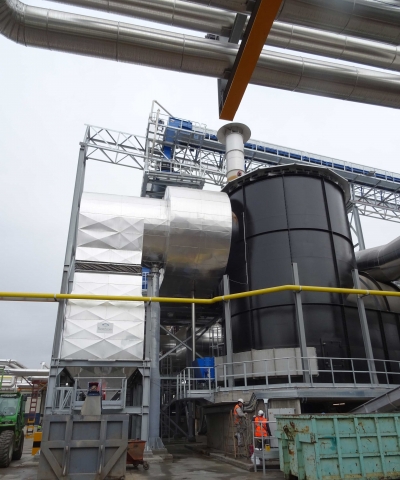
